Michigan Metal Coatings: The Ultimate Guide to Lasting Protection!
Protecting valuable assets from environmental degradation is a paramount concern for industries across Michigan. Effective solutions are essential to combat the relentless forces of corrosion and abrasion, which can compromise structural integrity and diminish operational efficiency. This comprehensive guide delves into the world of advanced michigan metal coatings, explaining how these specialized protective layers are applied to various substrates to significantly enhance durability and extend service life. Understanding the diverse formulations and precise application techniques is crucial for anyone operating in demanding industrial environments, seeking to ensure the long-term performance and resilience of their metal components.
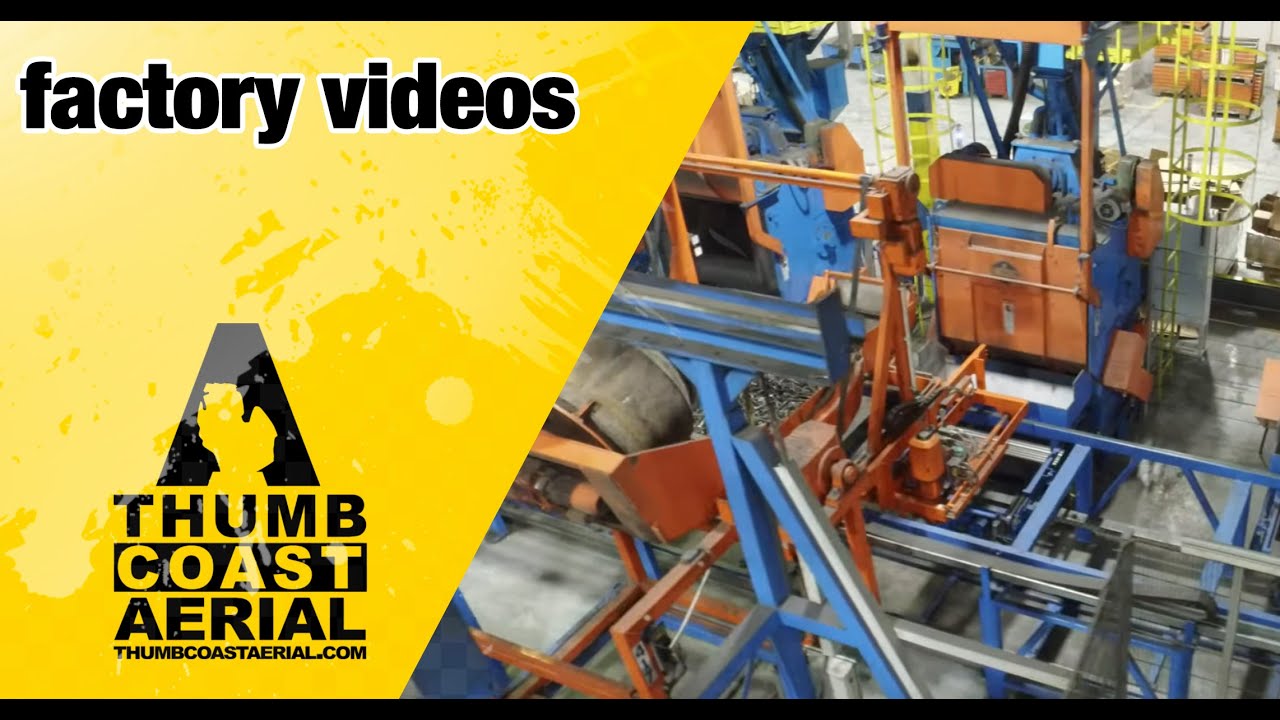
Image taken from the YouTube channel Thumb Coast Aerial & FPV , from the video titled Factory videos for Michigan Metal Coatings interior, promotional video footage Detroit MI. .
Michigan's industrial landscape, dominated by manufacturing, automotive, and burgeoning technology sectors, relies heavily on durable infrastructure and robust machinery. However, this economic powerhouse operates within a uniquely challenging environmental context. The Great Lakes State experiences dramatic seasonal shifts, from humid summers to harsh, snowy winters, often characterized by significant temperature fluctuations. The omnipresent moisture from the Great Lakes themselves, coupled with the liberal use of road salts during winter months, creates a highly corrosive environment for metals.
This relentless exposure to wear, tear, and environmental factors poses a substantial threat to assets, leading to premature degradation, costly downtime, and reduced operational efficiency. Ensuring the longevity and performance of critical equipment, vehicles, and structural components in such conditions is not merely a maintenance task; it is a strategic imperative for businesses and public entities across Michigan.
Michigan Metal Coatings: The Ultimate Defense
In the face of these formidable challenges, Michigan metal coatings emerge as a pivotal solution for achieving robust and lasting protection. These aren't just superficial applications; they are advanced, engineered barriers designed to shield underlying materials from the specific stressors prevalent in the Great Lakes State. From safeguarding precision automotive components to protecting heavy industrial machinery and public infrastructure, specialized metal coatings provide an invaluable line of defense.
These cutting-edge solutions go beyond mere aesthetics, actively preventing corrosion, abrasion, chemical degradation, and fatigue. By applying the right coating, businesses can dramatically extend the operational lifespan of their assets, reduce maintenance frequency, and significantly defer the need for costly replacements. It's an investment that pays dividends in sustained performance, enhanced safety, and long-term economic viability.
Your Comprehensive Guide to Protective Coatings
This comprehensive guide is designed to serve as your authoritative resource on advanced protective coatings tailored for Michigan's unique demands. We will delve into the diverse types of metal coatings available, exploring their distinct properties, applications, and suitability for various industrial environments. Readers will gain a clear understanding of the extensive benefits these coatings offer, including enhanced durability, improved operational efficiency, and substantial cost savings over an asset's lifecycle. Finally, we will illustrate practical applications across key Michigan industries, demonstrating how these sophisticated technologies are not just protecting individual assets but also bolstering the resilience of the state's economic backbone.
Having established the critical need for robust asset protection in Michigan's diverse industrial landscape and challenging climate, it's essential to understand the foundational solution: metal coatings. These specialized applications are not merely an add-on; they are the primary defense against the relentless forces of degradation that threaten the lifespan and performance of valuable assets across the Great Lakes State.
Understanding Metal Coatings: The Foundation of Lasting Protection
Metal coatings are engineered layers, often microscopic in thickness, applied to the surface of a metal substrate. Far from being a simple paint, these protective films are sophisticated formulations, leveraging various materials such as polymers, ceramics, and even other metals, meticulously designed to achieve specific protective properties. Their fundamental role is unequivocal: to preserve and extend the useful life of the underlying metal, transforming vulnerable surfaces into resilient defenses.
Why Michigan's Assets Depend on Protective Coatings
In Michigan, where the confluence of heavy industry, a demanding climate, and extensive infrastructure presents a unique set of challenges, these protective coatings are indispensable. The state's robust automotive, manufacturing, agriculture, and marine sectors operate amidst conditions that accelerate metal degradation:
- Harsh Winters: The pervasive use of road salts (calcium chloride, sodium chloride) on Michigan's vast network of roads and bridges is a primary driver of corrosion for vehicles, public infrastructure, and industrial equipment exposed to these elements.
- Industrial Environments: Factories and processing plants often expose machinery to abrasive particles, corrosive chemicals, and high temperatures, necessitating a durable protective layer.
- Great Lakes Proximity: The high humidity and consistent moisture associated with Michigan's extensive freshwater coastline create an ideal environment for rust and other forms of corrosion, impacting everything from docks and marine vessels to coastal infrastructure.
By applying high-performance metal coatings, businesses and municipalities in Michigan can significantly extend the lifespan of their industrial equipment, critical infrastructure (like bridges and pipelines), and even consumer goods. This not only safeguards initial investments but also enhances operational performance by preventing premature failure, reducing maintenance costs, and ensuring continued reliability.
The Core Principle: A Robust Barrier Against Degradation
At its core, the principle behind metal coatings is the creation of a robust, impervious barrier. This barrier acts as the first line of defense, physically separating the susceptible metal substrate from damaging environmental elements. Without this protective layer, exposed metal is vulnerable to:
- Corrosion: The electrochemical process that degrades metal, often seen as rust on iron, accelerated by moisture, oxygen, and salts.
- Abrasion: Wear and tear caused by friction from contact with other surfaces or airborne particles.
- Chemical Exposure: Damage from acids, bases, solvents, and other industrial chemicals.
- UV Radiation: Degradation caused by prolonged exposure to sunlight, which can weaken material bonds and lead to cracking or chalking.
- Impact Damage: While not always entirely preventable, certain coatings can enhance surface hardness, making the substrate more resistant to dings and scratches.
This impenetrable shield ensures lasting protection, preserving the structural integrity and aesthetic appearance of assets, which is critical for maintaining safety, functionality, and economic value across Michigan's diverse landscape.
Building upon the fundamental role of metal coatings in creating a robust barrier against degradation, it’s essential to explore why investing in high-performance solutions is not just beneficial, but critical for industrial longevity and operational efficiency. These advanced coatings offer a multifaceted defense that extends far beyond simple surface protection, delivering tangible economic and performance advantages.
The Paramount Benefits of High-Performance Metal Coatings
High-performance metal coatings are more than just a protective layer; they are a strategic investment that yields significant returns through enhanced asset life, reduced maintenance, and superior operational resilience. For Michigan's diverse industrial landscape—from automotive manufacturing to heavy machinery and chemical processing—these benefits translate directly into competitive advantage and long-term sustainability.
Lasting Protection: Extending Asset Life and Reducing Costs
One of the primary benefits of high-performance metal coatings is their ability to deliver lasting protection, significantly extending the operational life of valuable assets. By creating a durable shield against environmental stressors and wear, these coatings prevent premature degradation. This directly translates into reduced replacement costs for expensive machinery, infrastructure, and components.
Consider, for example, industrial equipment in a busy Michigan factory. A high-performance coating can double or even triple the lifespan of critical parts, deferring capital expenditure and minimizing disruptive downtime associated with repairs or replacements. This proactive protection strategy is far more cost-effective than reactive maintenance.
Corrosion Resistance and Rust Prevention: Battling Environmental Deterioration
Corrosion and rust are pervasive threats to metal, driven by exposure to moisture, oxygen, and various chemicals. These processes lead to material degradation, structural weakening, and eventually, component failure. The annual global cost of corrosion is estimated to be over $2.5 trillion, underscoring the immense economic impact it has across industries.
High-performance metal coatings act as an impermeable barrier, effectively preventing common forms of deterioration by isolating the metal substrate from corrosive elements. They combat oxidation, block moisture ingress, and disrupt the electrochemical reactions that lead to rust. For Michigan, where seasonal weather extremes and the widespread use of road salts create aggressive corrosive environments, superior corrosion resistance and rust prevention are not just advantages—they are necessities for preserving infrastructure and operational integrity.
Enhanced Durability: Strengthening Coated Surfaces
Beyond simply preventing decay, high-performance metal coatings intrinsically contribute to the overall strength and resilience of coated surfaces. They don't just sit on the surface; they bond with the substrate, creating a tougher, more robust composite structure. This enhancement means the metal can withstand greater stresses, impacts, and operational demands without compromising its integrity.
This increased durability helps prevent minor surface damage from escalating into major structural issues, maintaining optimal performance and safety standards for critical equipment and components throughout their extended service life.
Abrasion Resistance: Protecting Against Physical Wear
In many industrial applications, particularly those involving movement, friction, or material flow, abrasion resistance is paramount. High-performance coatings are engineered to protect against physical wear caused by rubbing, scraping, impact, and the constant flow of abrasive materials like sand, gravel, or even rapidly moving fluids.
For industrial applications common in Michigan—such as conveyor systems, agricultural machinery, mining equipment, and pump components—the ability of a coating to withstand continuous friction and impact is crucial. By minimizing material loss due to abrasion, these coatings maintain dimensional stability and operational efficiency, significantly extending the life of parts constantly subjected to harsh mechanical forces.
Chemical Resistance: Shielding Against Corrosive Agents
Many Michigan industries, including chemical manufacturing, automotive, and wastewater treatment, routinely handle a variety of corrosive chemicals, acids, alkalis, and solvents. Without adequate protection, these substances can rapidly degrade metal components, leading to leaks, equipment failure, and potentially hazardous situations.
High-performance metal coatings offer exceptional chemical resistance, forming a robust shield that prevents these aggressive substances from reaching and reacting with the underlying metal. This protection is vital for maintaining the structural integrity of tanks, pipes, valves, and processing equipment, ensuring operational safety and compliance in environments where chemical exposure is a daily reality.
Having explored the significant advantages that high-performance metal coatings offer, from extending asset life to providing robust resistance against corrosion and abrasion, it's clear that selecting the right coating is paramount. Michigan's diverse industrial landscape, characterized by varying environmental stressors and operational demands, necessitates a strategic approach to material protection. Now, let's delve into the specific types of advanced protective coatings widely utilized across the state, examining their unique compositions, application processes, and the unparalleled benefits they provide in ensuring lasting durability.
Key Types of Protective Coatings Driving Durability in Michigan
This section explores specific types of protective coatings widely used in Michigan. It details their compositions and application processes, highlighting the unique benefits of each, such as exceptional durability, crucial resistance properties, and suitability for various industrial applications, ensuring assets withstand harsh conditions.
Powder Coating
Powder coating is a dry finishing process that has gained immense popularity due to its environmental advantages and superior performance. Unlike traditional liquid coatings, powder coating involves the electrostatic application of a finely ground, dry pigment and resin powder onto a metal substrate. The electrically charged powder particles adhere to the grounded surface, forming a uniform layer. The coated part is then moved into a curing oven, where the powder melts and flows out to form a smooth, continuous film that chemically cross-links to create a highly durable finish.
This process is remarkably clean, as it emits virtually no Volatile Organic Compounds (VOCs) or Hazardous Air Pollutants (HAPs), making it an eco-friendly choice for many industrial applications in Michigan. Beyond its environmental benefits, powder coating delivers exceptional durability, offering superior abrasion resistance against wear from friction and impact. Its inherent flexibility also contributes to excellent chip resistance, ensuring the coating remains intact even under stress. Furthermore, powder coating offers a vast array of finishes, including various colors, textures, and gloss levels, providing both protective and aesthetic benefits for components ranging from automotive parts to heavy machinery and architectural elements.
Epoxy Coatings
Epoxy coatings are renowned for their robust polymer composition and are a cornerstone of protective solutions for demanding environments. These coatings are typically a two-part system, consisting of an epoxy resin and a polyamine hardener. When these two components are mixed, a chemical reaction occurs, initiating a curing process that transforms the liquid mixture into a rigid, plastic-like thermoset material. This unique chemical structure is what imparts epoxy coatings with their extraordinary properties.
The key advantages of epoxy coatings include outstanding chemical resistance, making them ideal for protecting surfaces against corrosive chemicals, acids, alkalis, and solvents commonly found in manufacturing plants, wastewater treatment facilities, and chemical processing industries across Michigan. They also provide excellent corrosion resistance by forming an impermeable barrier that prevents moisture and oxygen from reaching the metal substrate, thereby combating rust and other forms of deterioration. Coupled with their high adhesion capabilities, which ensure a strong bond to various surfaces, epoxy coatings offer exceptional resilience in harsh, demanding environments, making them ideal protective coatings for industrial floors, tanks, pipes, and structural steel where long-term durability and resistance are paramount.
While understanding the diverse protective coatings available for Michigan's industrial landscape is crucial, the effectiveness of even the most advanced coating hinges entirely on a less visible, yet profoundly critical, stage: surface preparation.
The Imperative Role of Surface Preparation for Optimal Adhesion and Lasting Protection
In the realm of industrial metal coatings, the adage "you can't build a strong house on a weak foundation" holds absolute truth. The success, longevity, and protective efficacy of any metal coatings application are fundamentally reliant on meticulous surface preparation. This initial, often undervalued, phase is the true cornerstone, dictating whether a coating will merely sit on a surface or form a robust, lasting bond.
The High Cost of Neglecting Preparation
Neglecting this foundational step is a primary driver of premature coating failure, directly compromising lasting protection and durability. Industry analyses consistently reveal that a significant majority—often cited as high as 70-80%—of coating failures can be traced back to insufficient or improper surface preparation. Without proper preparation, even the highest quality industrial coatings will struggle to form a strong bond with the substrate. This can lead to a cascade of issues, including:
- Adhesion Loss: The coating delaminates, flakes, or peels off.
- Blistering and Bubbling: Trapped contaminants or moisture cause pockets to form under the coating.
- Premature Corrosion: Inadequate cleaning leaves corrosive agents on the surface, allowing rust to form beneath the new coating.
- Reduced Lifespan: The protective system fails long before its expected service life, leading to costly reapplication and downtime.
These failures undermine the very purpose of applying a protective coating, negating initial investments and exposing valuable assets to Michigan's harsh environmental conditions.
Essential Surface Preparation Techniques
Achieving optimal adhesion and long-term performance requires a systematic approach to surface preparation. Several key techniques are employed to create an ideal substrate, free of contaminants and with a suitable profile for bonding.
Cleaning and Degreasing
The first step in any preparation process involves the thorough removal of surface contaminants. This includes:
- Grease and Oil: Industrial lubricants, fingerprints, and other organic residues can prevent proper wetting and bonding of the coating. Solvents, detergents, and alkaline cleaners are typically used.
- Dirt and Dust: Loose particles can create weak points in the coating.
- Old Paint/Coatings: Depending on the new coating system, existing paint may need to be entirely removed or simply cleaned and roughened.
Effective cleaning ensures the coating adheres directly to the metal, not to a layer of foreign material.
Abrasive Blasting: Creating the Ideal Profile
Once cleaned, the most common and effective method for preparing metal surfaces is abrasive blasting (often referred to as sandblasting or shot blasting). This technique propels abrasive media at high velocity against the surface, achieving several critical objectives:
- Rust and Scale Removal: It effectively strips away existing rust, mill scale, and old coatings, exposing clean, bare metal.
- Surface Profiling: The impact of the abrasive media creates a microscopic "anchor pattern" or profile on the metal surface. This roughened texture provides increased surface area and mechanical "teeth" for the coating to grip onto, dramatically enhancing adhesion. The depth and density of this profile are crucial and vary depending on the type of coating to be applied.
- Contaminant Removal: Any remaining embedded contaminants are dislodged.
Common abrasive media include sand, steel grit, steel shot, garnet, and plastic beads, each chosen based on the desired surface profile, material being blasted, and environmental considerations. The standard of cleanliness and profile achieved is often measured against industry specifications, such as those set by NACE International (formerly the National Association of Corrosion Engineers) or SSPC (The Society for Protective Coatings).
By adhering to these meticulous surface preparation protocols, industrial operations in Michigan can significantly enhance the performance and longevity of their metal coatings, ensuring unparalleled durability and lasting protection against the elements.
Having established that meticulous surface preparation is the non-negotiable cornerstone for successful metal coating application, ensuring optimal adhesion and long-term performance, the next critical step involves a strategic approach to selecting the ideal coating. Even the most perfectly prepared surface will fail to deliver lasting protection if the chosen coating is ill-suited to its operating environment and demands.
Strategic Selection: Choosing the Right Michigan Metal Coatings for Your Industrial Needs
Choosing the most appropriate metal coating is a nuanced process that directly impacts the longevity, performance, and cost-effectiveness of your industrial assets. It requires a deep understanding of both the environment the asset will operate in and the specific demands placed upon it. A "one-size-fits-all" approach to industrial coatings is often inadequate, leading to premature failure and costly repairs.
Key Factors for Optimal Coating Selection
To ensure maximum lasting protection and durability, the selection process must meticulously consider several pivotal factors:
Environmental Exposure
Michigan's unique climate presents significant challenges that directly impact coating longevity. The state experiences severe winters, characterized by freezing temperatures, heavy snowfall, and the widespread use of corrosive road salts (e.g., sodium chloride, calcium chloride), which can aggressively attack metals. Furthermore, the proximity to the Great Lakes contributes to high humidity levels, particularly during summer months, increasing the risk of condensation and subsequent corrosion. Industrial areas may also face exposure to atmospheric pollutants. Therefore, coatings chosen for applications in Michigan must offer robust protection against these diverse environmental stressors.
Operational Stresses
Beyond the natural environment, the daily demands placed on an industrial asset dictate specific coating requirements. Consider factors such as:
- Abrasion: Components subjected to constant friction, impact from materials, or heavy traffic.
- Impact: Risk of accidental collisions, dropping tools, or heavy loads.
- Temperature Fluctuations: Exposure to extreme heat or cold, or rapid temperature cycling common in manufacturing processes.
- Chemical Exposure: Contact with acids, alkalis, solvents, oils, fuels, or other corrosive chemicals.
Desired Aesthetic and Specific Performance Requirements
While protection is paramount, the visual appearance of a coated asset can also be important, whether for branding, safety marking, or integration into a larger design. Beyond aesthetics, precise performance needs must be identified:
- High Corrosion Resistance: Essential for combating rust and degradation, particularly critical in Michigan's climate. Coatings like zinc-rich primers, epoxies, and polyurethanes are often selected for their superior anti-corrosive properties.
- Specific Chemical Resistance: If the asset will regularly encounter particular chemicals, the coating must be formulated to withstand their corrosive or degradative effects without compromise.
- Superior Abrasion Resistance: For high-wear applications, coatings engineered for hardness and durability are crucial. Examples include ceramic-reinforced coatings or specialized polyureas.
- Other considerations may include UV stability, electrical conductivity or insulation, non-stick properties, or even thermal management.
Tailoring Metal Coating Solutions for Michigan's Diverse Industries
Michigan is home to a vast array of industries, each with distinct operational environments and regulatory requirements. A tailored approach to metal coating solutions is not merely beneficial; it is essential for ensuring maximum lasting protection and durability. For instance:
- Automotive Manufacturing: Components often require coatings that withstand high temperatures, frequent chemical exposure (e.g., greases, brake fluids), and significant abrasion.
- Infrastructure (Bridges, Pipelines): Long-term corrosion protection against weather, de-icing salts, and soil conditions is paramount, requiring durable, long-life systems.
- Marine (Great Lakes): Vessels and dock structures demand coatings with exceptional resistance to freshwater corrosion, UV degradation, and often, anti-fouling properties to prevent biological growth.
- General Manufacturing: Equipment may need coatings that offer a blend of chemical, impact, and abrasion resistance to withstand demanding production cycles.
By meticulously evaluating these factors and collaborating with experienced coating specialists, businesses across Michigan can confidently select metal coating solutions that are precisely engineered for their unique industrial needs, guaranteeing optimal performance, extending asset lifespan, and ultimately, reducing long-term maintenance costs.
Having understood the critical factors in selecting the appropriate metal coating for specific industrial demands, it’s equally important to explore how these specialized coatings are put to work across Michigan’s diverse economic landscape. The application of advanced metal coatings is not a one-size-fits-all solution but a strategic deployment that addresses unique challenges in various sectors, enhancing durability and ensuring lasting protection for vital assets.
Diverse Applications of Metal Coatings Across Michigan's Industries
Michigan's robust industrial backbone, ranging from automotive giants to intricate general fabrication shops, consistently relies on specialized metal coatings to ensure the longevity and peak performance of its products and infrastructure. These coatings are indispensable in combating the state’s challenging environmental conditions, such as severe winters and fluctuating humidity, as well as the operational stresses inherent in various industrial processes.
Automotive Sector: Driving Durability and Aesthetics
The automotive industry, a cornerstone of Michigan’s economy, presents a prime example of the critical need for advanced metal coatings. Vehicles are exposed to relentless wear and tear, from abrasive road salt and moisture to impacts and temperature extremes. Specialized coatings are vital for:
- Corrosion Resistance: Components like chassis, brake lines, and underbody parts are often treated with zinc plating, e-coating (electrophoretic deposition), or powder coating to withstand road salts and humidity, preventing rust that could compromise safety and structural integrity.
- Abrasion Resistance: Engine components, suspension parts, and certain interior elements benefit from coatings that resist friction and wear, extending their operational life.
- Aesthetics and Finish: From protective clear coats on alloy wheels to decorative finishes on interior trim, coatings provide the desired look while offering protection against scratches and UV exposure. The demand for both functional and visually appealing coatings is paramount in this competitive sector.
Heavy Machinery and Equipment: Built to Endure
Michigan is home to manufacturers of heavy machinery used in construction, agriculture, and mining. Equipment in these sectors faces extreme conditions, including exposure to dirt, chemicals, impact, and continuous vibration. Metal coatings are essential for:
- Impact and Abrasion Protection: Excavator buckets, bulldozer blades, and tractor components are often coated with highly durable urethane or epoxy-based systems to resist chipping, scratching, and gouging from abrasive materials.
- Chemical Resistance: Agricultural machinery frequently encounters fertilizers and pesticides, while industrial equipment may be exposed to oils and solvents. Specialized coatings protect against chemical degradation, maintaining structural integrity.
- Weatherproofing: Given Michigan’s varied climate, heavy machinery requires robust coatings that can withstand extreme temperatures, UV radiation, and moisture, preventing rust and degradation that could lead to costly downtime.
Infrastructure: Protecting Michigan's Foundations
The state's infrastructure, encompassing bridges, pipelines, water treatment facilities, and public buildings, represents a massive investment that requires constant protection. Metal coatings play a vital role in ensuring the long-term integrity of these critical assets:
- Corrosion Control for Bridges: Steel components in Michigan’s extensive bridge network are highly susceptible to rust from road salt and moisture. Zinc-rich primers followed by durable epoxy or urethane topcoats provide multi-layered protection, extending the lifespan of these vital structures.
- Pipeline Integrity: Pipelines transporting water, oil, or gas often run underground or through varying environments. Coatings protect them from soil corrosion, microbial attack, and chemical interactions, preventing leaks and ensuring safe delivery.
- Structural Steel Protection: Large industrial buildings, sports arenas, and public facilities utilize structural steel that requires robust coating systems to resist environmental factors and provide fire resistance in some applications.
General Fabrication: Versatility for Diverse Needs
Michigan's general fabrication shops serve a wide array of industries, producing custom metal components, tools, and specialized equipment. The diversity of these products necessitates equally versatile coating solutions:
- Custom Tooling and Fixtures: Precision tools and manufacturing fixtures require coatings that offer enhanced hardness, wear resistance, and sometimes even low friction to improve operational efficiency and lifespan.
- Industrial Components: From complex prototypes to production-run parts, general fabrication benefits from coatings that can be precisely applied for specific functions, whether it's anodizing for aluminum parts for a durable, aesthetically pleasing finish, or phosphate coatings for improved paint adhesion and minor corrosion resistance.
- Consumer Goods: Even in consumer-facing products manufactured in Michigan, metal coatings ensure durability, safety, and an attractive finish, from household appliances to recreational equipment.
Across all these sectors, the strategic application of metal coatings is a testament to Michigan's commitment to durability, efficiency, and the longevity of its industrial assets. By addressing the unique environmental and operational challenges each industry faces, these coatings provide the lasting protection critical for economic vitality.
While understanding the diverse applications of metal coatings across Michigan's industries highlights their initial value, their true impact on asset preservation is realized through diligent maintenance. Ensuring that these specialized coatings continue to deliver peak performance and lasting protection requires a proactive approach to care.
Ensuring Longevity: Maintenance and Care for Enduring Lasting Protection
The lifespan and effectiveness of any industrial coating system are not solely determined by its initial application. Ongoing maintenance and timely interventions are paramount to maximizing the investment in metal coatings and preserving the integrity of critical assets. Implementing a robust maintenance strategy can significantly extend the durability of coated surfaces, preventing premature degradation and costly repairs.
Best Practices for Ongoing Coating Maintenance
Regular, systematic care is the cornerstone of extending the lifespan of metal coatings. The specific maintenance regimen will depend on the type of coating, the environmental conditions it endures, and the operational demands placed on the coated asset.
Key best practices include:
- Regular Cleaning: Removing dirt, dust, grime, chemicals, and other contaminants prevents them from accumulating and potentially compromising the coating's surface. For most industrial coatings, a simple wash with mild soap and water followed by a thorough rinse is often sufficient. However, for specialized coatings exposed to aggressive chemicals or high temperatures, specific cleaning agents and methods might be required to avoid damaging the coating.
- Avoid Abrasive Materials: When cleaning or working around coated surfaces, it's crucial to avoid harsh abrasive brushes, pads, or strong chemical solvents that could scratch, thin, or degrade the coating layer. This preserves the surface integrity and protective qualities.
- Adherence to Manufacturer Guidelines: Every coating system has unique properties and care requirements. Always consult the coating manufacturer's recommendations for cleaning agents, frequency, and specific environmental considerations to ensure optimal maintenance.
Consistent adherence to these practices can dramatically reduce the rate of wear and tear, ensuring the metal coatings provide continuous lasting protection.
The Critical Role of Regular Inspections
Proactive inspection is an indispensable element of asset preservation. Small issues can rapidly escalate into significant problems if left unaddressed. Regular inspections allow for the early detection of wear or damage to protective coatings, enabling timely intervention before extensive repairs become necessary.
During inspections, pay close attention to:
- Visual Cues: Look for any signs of cracking, chipping, blistering, peeling, discoloration, or dulling of the coating. These often indicate a breakdown in the coating's integrity.
- Corrosion Indicators: Even if the coating appears intact, look for signs of rust bleeding from underneath the coating, which could point to hidden damage or inadequate adhesion.
- Impact Points: Assets in active use are prone to minor impacts. Inspect edges, corners, and areas subject to friction or abrasion, as these are common points of initial failure.
The frequency of inspections should be tailored to the asset's environment and operational demands. High-stress or corrosive environments may necessitate weekly or monthly checks, while less demanding applications might suffice with quarterly or annual evaluations. The goal is to catch issues when they are minor, preserving the durability and protective capacity of the entire system.
Strategies for Minor Repairs
Even with the best maintenance and inspection protocols, minor damage can occur. Having a strategy for localized, minor repairs is crucial for preserving the overall integrity and durability of the coating system, ensuring continuous lasting protection.
Effective minor repair strategies typically involve:
- Immediate Action: Address small chips, scratches, or areas of localized corrosion as soon as they are detected. Delaying repairs allows damage to spread, compromising larger areas and potentially leading to substrate corrosion.
- Proper Surface Preparation: Before any touch-up, the damaged area must be meticulously cleaned and prepared. This often involves gently sanding or abrading the affected spot and the surrounding sound coating to ensure proper adhesion of the new material. Removing all rust, loose paint, and contaminants is critical.
- Material Compatibility: Always use a repair coating that is chemically compatible with the existing coating system. Using incompatible materials can lead to adhesion issues, blistering, or premature failure of the repair. Reputable coating manufacturers offer touch-up kits or repair procedures for their specific products.
- Careful Application: Apply the repair coating according to the manufacturer's instructions, paying attention to thickness and curing times. Proper application ensures the repair seamlessly integrates with the existing coating and provides the necessary protection.
By diligently applying these maintenance and repair strategies, businesses across Michigan can significantly extend the operational life of their coated assets, safeguarding their investments and ensuring metal coatings deliver enduring lasting protection for years to come.
Video: Michigan Metal Coatings: The Ultimate Guide to Lasting Protection!
We hope this guide has shed light on the critical role of these protective layers in safeguarding your assets. Remember, investing in quality michigan metal coatings is not just about protection; it's about ensuring longevity and peak performance for years to come.
Related Posts:
- Master Michigan Pull Tabs: Your Ultimate Guide to Rules and Wins!
- Michigan Ballot Status: Check Yours Now & Secure Your Vote!
- Westland Michigan Weather Radar: Your Real-Time Safety Guide
- State of Michigan Foster Care Payments: Maximizing Your Support
- Is The Orchards Michigan – Roseville Your Perfect Living Space?